Carbon Recycling International (CRI) has pioneered a process to transform CO2 emissions into methanol by direct hydrogenation of captured CO2. It now plans to deploy its technology at commercial scale and help curb emissions from the chemicals sector
The chemical industry is essential to the global economy, converting raw materials into countless every-day products. Accounting for about 14% of the world’s oil demand, chemicals and petrochemicals represent the world’s most energy-intensive industry segments, according to figures from the IEA. With about 90% of their energy derived from oil and gas, these industries alone are responsible for 5% of global CO2 emissions, emitting more than a 1.5bn t of CO2 into Earth’s atmosphere every year. In the absence of alternative processes, chemicals and petrochemicals are poised to increase oil demand by more than 30% by 2030. In line with international climate mitigation treaties and targets, the surging oil demand from the chemical sector calls for immediate action to transition towards more environmentally-benign feedstocks.
Greening chemicals with renewables and recycled value chains
Unlike other sectors of the economy, the chemicals industry cannot be fully decarbonised since it relies on carbon-based chemistry and many of its essential products are hydrocarbon derivatives. An alternative source of hydrocarbon raw materials is therefore needed. One method to achieve the goal of sourcing more sustainable and climate-friendly chemicals is through the production of bio-based materials in so called bio-refineries. The sheer size of the petrochemical industry and known limitations to sustainable sourcing of biomass at large scales makes this a challenging, if not impossible task to achieve by relying on biomass alone. So, what other ways are there to ‘greening’ the chemical sector? Is it possible to move towards a more circular economy by recycling the carbon rather than extracting or harvesting it?
One of the key basic chemicals produced globally is methanol. At over 80m t/y of production in 2018, only ethylene and propylene exceed it in terms of annual production for organic basic chemicals. The reason for this is that methanol plays an integral role in the chemical industry as ‘C1’ feedstock for production of chemical intermediates such as formaldehyde and acetic acid which in turn are used to produce everyday items like paint, adhesives and plastics. An early way to produce methanol was by the destructive distillation of wood, giving it the name wood alcohol. In the modern era, methanol has been predominantly produced from natural gas, oil or coal. With consumption steadily increasing, methanol production has increased dependence on fossil energy resources and results in significant emissions of greenhouse gases. Curbing this trend will require more sustainable production using renewable energy resources and feedstocks.
Production and use of eMethanol in the chemical sector
Since 2012, CRI has been pioneering a different approach based on producing methanol from CO2 and renewable energy. This process has been realised at industrial scale at the company’s pilot and demonstration plants in Iceland, where methanol is produced by catalytically reacting CO2 extracted from a waste gas stream, with hydrogen generated from water electrolysis using renewable power. With electrolytically-derived hydrogen at its core, production of renewable methanol or eMethanol as it is also called, provides an alternative pathway for storing and using clean and renewable energy in chemicals.
Conventional production of methanol results in emissions from resource extraction, processing and production. This ranges from 0.7 t of CO2 per 1 t of methanol produced at modern production plants based on natural gas reforming (https://bit.ly/2O3SkvB) to over 3 t of CO2 for production plants using coal gasification (http://doi.org/ddzm). In contrast, producing methanol from CO2 captured from industrial emissions consumes more than 1.3 t of CO2 for every 1 t of methanol produced. CRI’s demonstration plant in Svartsengi was the first facility based on carbon capture and utilisation (CCU) technology to receive certification according to the International Sustainability and Carbon Certification (ISCC), a widely used system to certify sustainability for biofuels.
In addition to the conventional applications for methanol as a chemical intermediate, one of the more promising emerging opportunities to reduce the share of fossil fuel derived petrochemicals is in production of light olefins via the methanol-to-olefins (MTO) process. The use of the MTO process to produce ethylene and propylene has grown substantially in recent years and according to figures from IHS Markit now represents about 15% of global methanol demand. The MTO pathway using eMethanol offers a direct feedstock alternative to oil, coal or natural gas for production of plastics. Similarly, the production of aromatics from eMethanol, to produce more complex intermediates or solvents such as benzene, toluene and xylene, provides a further opportunity to alternatives traditionally produced from oil. A large portion of plastics are virgin materials which are not source separated or cannot be recycled at the end of their useful life and end up as part of our municipal solid waste that goes to landfill or incineration. Capturing the CO2 from waste incineration and using it to produce methanol can, in effect lead to a form of recycling, reduce the need for virgin materials, and create a more circular economy.
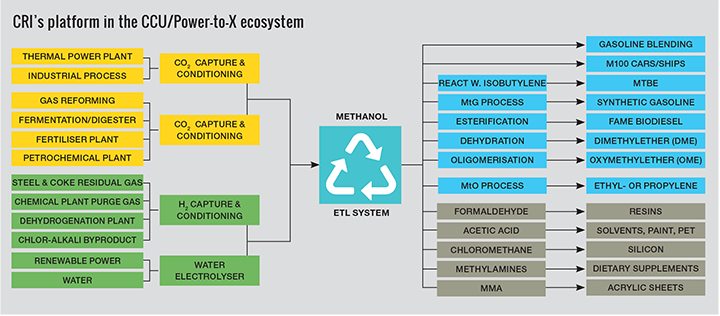
Green consumerism and social responsibility
In the absence of effective government mandates or regulations that either require or incentivise chemical producers to source sustainable raw materials, future demand for eMethanol or bio-methanol in the sector is driven by voluntary initiatives from manufacturers and/or end-consumer demand for more sustainable products. According to Deloitte’s Global Millennial Survey 2019, 42% of consumers aged 21-35 said that they initiate or deepen a consumer relationship based on how they perceive the environmental impact of the product. This rise of green consumerism presents an interesting opportunity for chemical producers. As demand increases for products with low carbon footprints, so does demand for feedstocks and processes which yield lower lifecycle emissions. Ingólfur Guðmundsson, CEO of CRI, says: “Producers of synthetic materials are beginning to capitalise on this development by gradually shifting to renewable raw materials like eMethanol, competitively offering greener products.”
He adds that “the possibility of gradual or partial adoption of the product into the existing value-chains allows producers to achieve large environmental and economic benefits at moderate costs.”
CRI’s demo plant in Iceland serves as a model for the state of the technology which CRI now plans to increase to commercial scale. CRI has already identified several sites, laying the groundwork for large-scale adoption of its technology. The first commercial plant in Europe is planned for commissioning in 2022 with more to follow. Sourcing large volumes of carbon neutral eMethanol will provide an opportunity for downstream chemical producers to differentiate their products from conventional ones and meet sustainability targets. Guðmundsson says that “although most of the demand for eMethanol is currently from developments in the European fuel market, we anticipate demand from the chemicals industry to increase in the coming years. It seems inevitable that to address society’s need for essential materials and chemicals, and at the same time protect our climate, we will need to employ recycled carbon value-chains.”
December 12, 2019
Article by Carbon Recycling International (CRI)
Originally published by The Chemical Engineer